A workflow is a reliably repeatable pattern of activity enabled by a systematic organization of resources, defined roles and mass, energy and information flows, into a work process that can be documented and learned. Workflows are always designed to achieve processing intents of some sort, such as physical transformation, service provision, or information processing.
Workflows are closely related to other concepts used to describe organizational structure, such as silos, functions, teams, projects, policies and hierarchies. Workflows may be viewed as one primitive building block of organizations. The relationships among these concepts are described later in this entry.
Related concepts
Workflows are a distinctly modern phenomenon. While one might imagine individual efforts in rational organization of labor in the construction of historical artifacts such as the pyramids, the idea that one can create value by studying the nature of work itself and organizing it better is a distinctly modern one that should probably be attributed to Adam Smith. It is easiest to understand the development of the notions of workflow in terms of loosely defined eras, with a great deal of overlap.
Beginnings in Manufacturing (1900-1950): Notions of workflow are best understood in terms of the historical development of the conceptualization of work itself. The modern history of workflows can be traced to F. W. Taylor (Taylor, 1919) and H. Gantt. Together they launched the study of the deliberate, rational organization of work, in the context of manufacturing. The types of workflow of concern to Taylor and his contemporaries primarily involved mass and energy flows, and these were studied and improved using time and motion studies. Information-based workflows, however, did begin to grow in the same era. A particularly influential figure was Melvil Dewey who, besides inventing the eponymous Dewey Decimal System, was also responsible for the development of the hanging file folder. While the assembly line remains the most famous example of a workflow from this era, the early thinking around work was far more sophisticated than is commonly understood, and the notion of flow was more than a sequential breakdown of processing. The common conceptual models of modern operations research, including flow shops, job shops and queuing systems (Pinedo, 2001) can be found in evolved forms in early 20th century industry. That said, this early era was still limited by its relatively inflexible notions of information flow and thus is identified with the simplest notions of workflow optimization and productivity: throughput and resource utilization. The cultural impact of this era of workflows can be understood through films such as Chaplin's classic Modern Times. These concepts did not stay confined to the shop floor (one magazine invited housewives to puzzle over the fastest way to toast three slices of bread on a one-side, two-slice grill). The popular cheaper by the dozen introduced the emerging concepts to the context of family life.
Maturation and Growth (1950-1980): The invention of the typewriter and the copier allowed the principles of rational organization of labor, first discovered in the manufacturing shop floor. Paper, filing systems and sophisticated systems of managing physically manifest information flows evolved. Alongside this increasing scope of formalized workflows to information work, two other events provided a huge impetus for the development of thought around workflows. These were the development of mathematical optimization techniques and the maturation of the field of optimization and the impact of World War II and the Apollo program, both unprecedented in their demands for the rational organization of work. In cultural terms, the classic management tome, The Organization Man documented the nature of work in this era.
The Quality Era (1980-1995): By 1980 two glaring flaws in the nature of the supposedly scientific organization of workflows became apparent. The first was that the methods pioneered by Taylor only applied to humans conceptualized as one-dimensional automatons. Considered in the light of human needs for self-actualization, creative engagement in work and growth (the Maslow hierarchy became a popular tool in this critique), the classical industrial-style organization of work was critiqued as being both dehumanizing and suboptimal in its use of the potential of human beings. The second critique had to do with quality. Workflows conceptualized to be rational with respect at a given time, even with the best of intentions, were understood to acquire inertia and rigidity, rendering them irrational with respect to changing work conditions. The first critique did not gain much traction other than acknowledgement as an issue, but quality, in both analytic and synthetic manifestations, transformed the nature of work through a variety of movements ranging from total quality management to six sigma to more qualitative notions of business process re-engineering (Hammers and Champy, 1991). Under the influence of the quality movement, workflows became the subject of much scrutiny and optimization efforts. Acknowledgement of the dynamic and changing nature of the demands on workflows came in the form of recognition of the phenomena associated with critical paths and moving bottlenecks (Goldratt, E., 1996).
The Information Era (1990 - 2002): The experiences with the quality movement made it clear that information flows are fundamentally different from the mass and energy flows which inspired the first forms of rational workflows. The low cost and adaptability of information flows were seen as enabling workflows that were at once highly rational in their organization and highly flexible, adaptable and responsive. These insights unleashed a whole range of information technology at workflows in manufacturing, services and pure information work. Flexible manufacturing systems, just in time inventory management and other highly agile and adaptable systems of workflow are products of this era.
The Virtual Workflow Era (2002): The Internet bust of the early years of the 21st century led to a period of caution towards ambitious conceptualizations of smart workflows. Today, a variety of actors in the economy are returning to a consideration of the problem of developing models of work that are at once rational, flexible and capable of taking advantage of globalization, distributed work practices, while allowing the humans embedded in them to realize their full creative potential. Among the most exciting developments are the serious thought given to apparently anarchic systems of organization that have evolved in the open source software community.
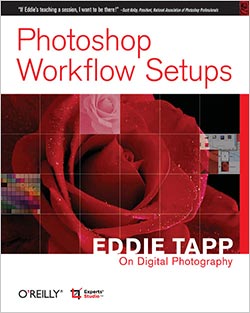
The following examples illustrate the variety of workflows seen in various contexts:
In military planning, a Concept of Operations (CONOPS) is a workflow that defines particular mission types
In machine shops, particularly job shops and flow shops, the flow of a part through the various processing stations is a work flow
Insurance claims processing is an example of an information-intensive, document-driven workflow
Wikipedia editing is an example of a stochastic workflow
The Getting Things Done (GTD) system is a model of personal workflow management for information workers Features and phenomenology
The key driver to gain benefit from the understanding of the workflow process in a business context is that the throughput of the workstream path is modelled in such a way as to evaluate the efficiency of the flow route through internal silos with a view to increasing discrete control of uniquely identified business attributes and rules and reducing potential low efficiency drivers. Evaluation of resources, both physical and human is essential to evaluate hand-off points and potential to create smoother transitions between tasks. Several workflow improvement theories have been proposed and implemented in the modern workplace. These include:
As a way of bridging the gap between the two, significant effort is being put into defining workflow patterns that can be used to compare and contrast different workflow engines across both of these domains.
Six Sigma
Total Quality Management
Business process reengineering
Lean systems Workflow improvement theories
A workflow can usually be described using formal or informal flow diagramming techniques, showing directed flows between processing steps. Single processing steps or components of a workflow can basically be defined by three parameters:
Components can only be plugged together if the output of one previous (set of) component(s) is equal to the mandatory input requirements of the following component. Thus, the essential description of a component actually comprises only in- and output that are described fully in terms of data types and their meaning (semantics). The algorithms' or rules' description need only be included when there are several alternative ways to transform one type of input into one type of output - possibly with different accuracy, speed, etc..
Especially when the components are non-local services that are invoked remotely via a computer network, like Web services, additional descriptors like QoS, availability, etc. have to be considered, too.
input description: the information, material and energy required to complete the step
transformation rules, algorithms, which may be carried out by associated human roles or machines, or a combination
output description: the information, material and energy produced by the step and provided as input to downstream steps. Workflow components
Main article: Workflow application
Many software systems to support workflows in particular domains exist. Such systems manage tasks such as automatic routing, partially automated processing and integration between different functional software applications and hardware systems that contribute to the value-addition process underlying the workflow.
See also
No comments:
Post a Comment